01 METZ RACING TEAM
Type of project – 2024
As a member of the ENI Metz Racing Team, I contributed to the design, simulation, manufacturing, and testing of a Formula Student single-seater race car. This experience required interdisciplinary collaboration, precision engineering, and adherence to tight deadlines in a competitive international environment. Through my roles in the undercarriage department, I developed and applied advanced skills in mechanical design, structural analysis, manufacturing, and project management, contributing to the team's notable successes across multiple competitions.
1. Mechanical Design & CAD

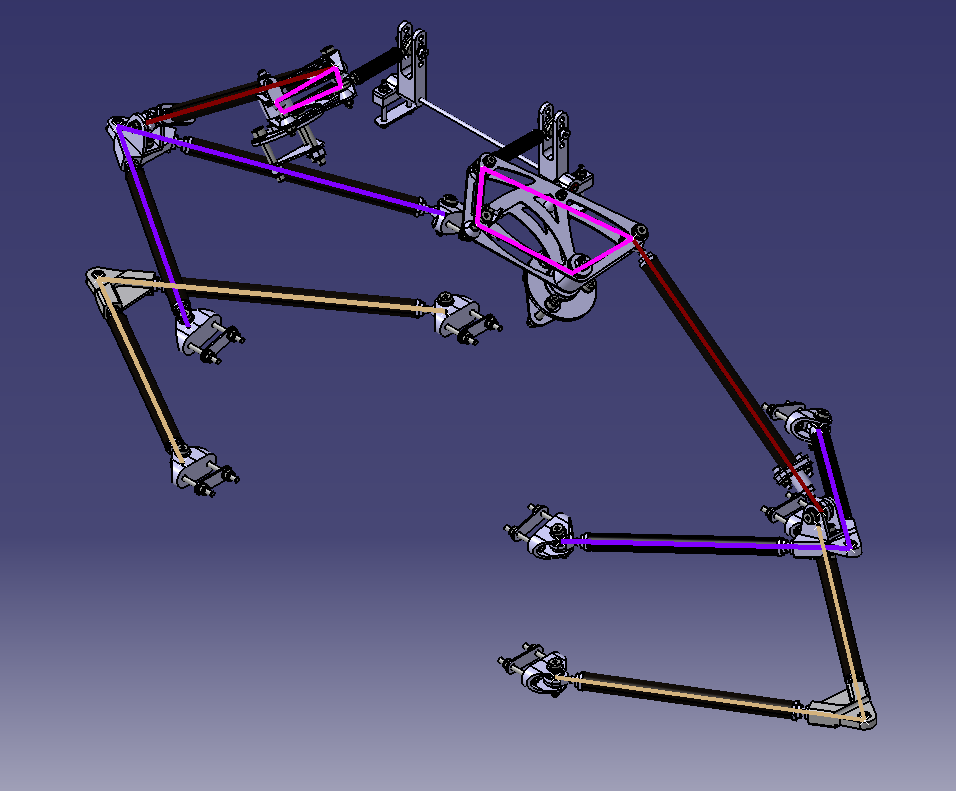


I played a critical role in designing the undercarriage components, ensuring optimal performance and compliance with Formula Student rules. Using Catia V5 R20, I created precise 3D models, including an adjustable wire skeleton to optimize geometry for vehicle dynamics.
- Defined and implemented specifications for 17 interconnected suspension parameters (toe, camber, caster, etc.).
- Designed critical components such as adjustable suspension arms and upright prototypes.
- Maintained an organized Bill of Materials (BOM) for materials, manufacturing processes, and cost management.
- Built 3D-printed prototypes to verify component fit and identify potential design conflicts.
2. Structural Analysis & Simulation
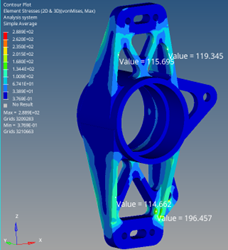

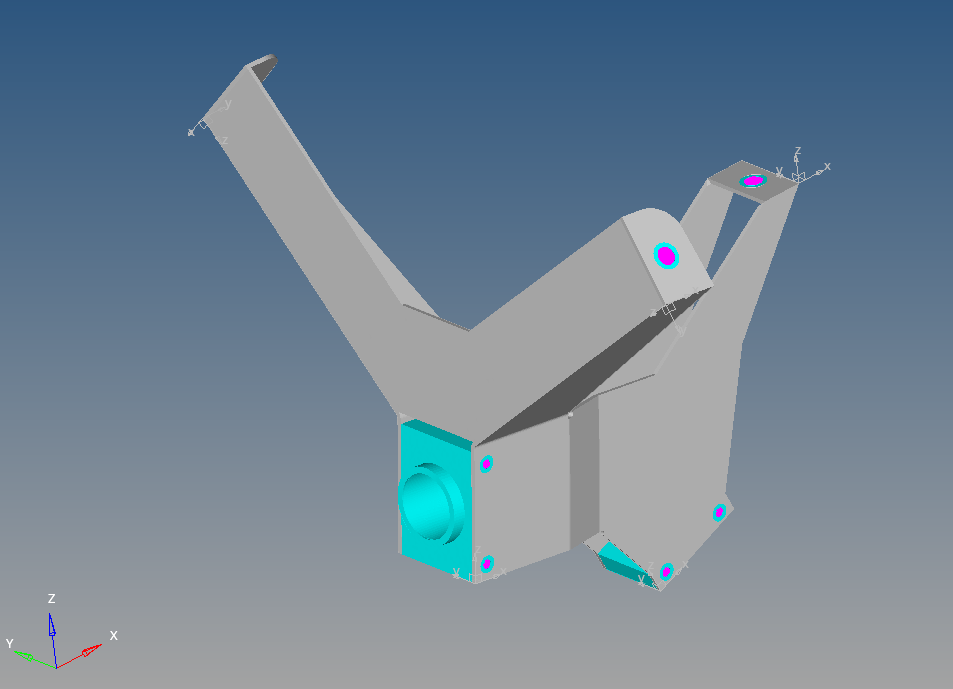

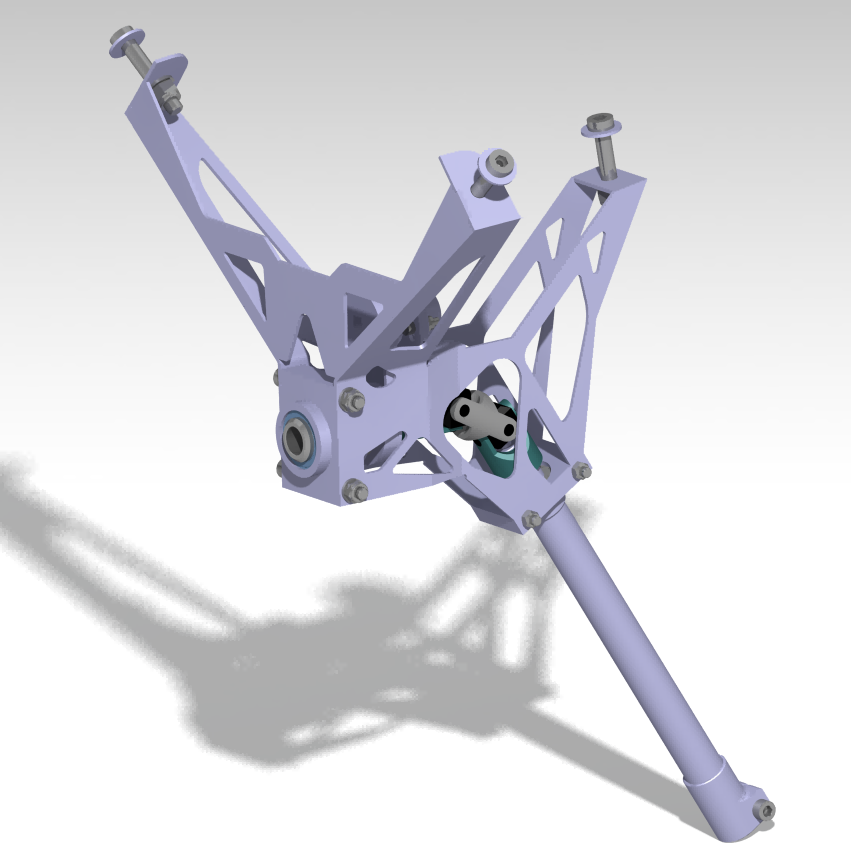
To ensure safety and reliability, I conducted structural simulations on critical components, focusing on strength, weight optimization, and rule compliance.
- Performed static analysis using HyperMesh 2022 to validate components against safety standards (Von Mises stress with safety factor of 2).
- Developed load cases for dynamic scenarios (turning, braking, combined movements) to analyze stress on key components like uprights and hubs.
- Executed topology optimization to reduce weight, saving up to 400g per component, while ensuring mechanical integrity.
- Verified optimized designs through additional static analysis to confirm durability and performance.
3. Manufacturing & CAM


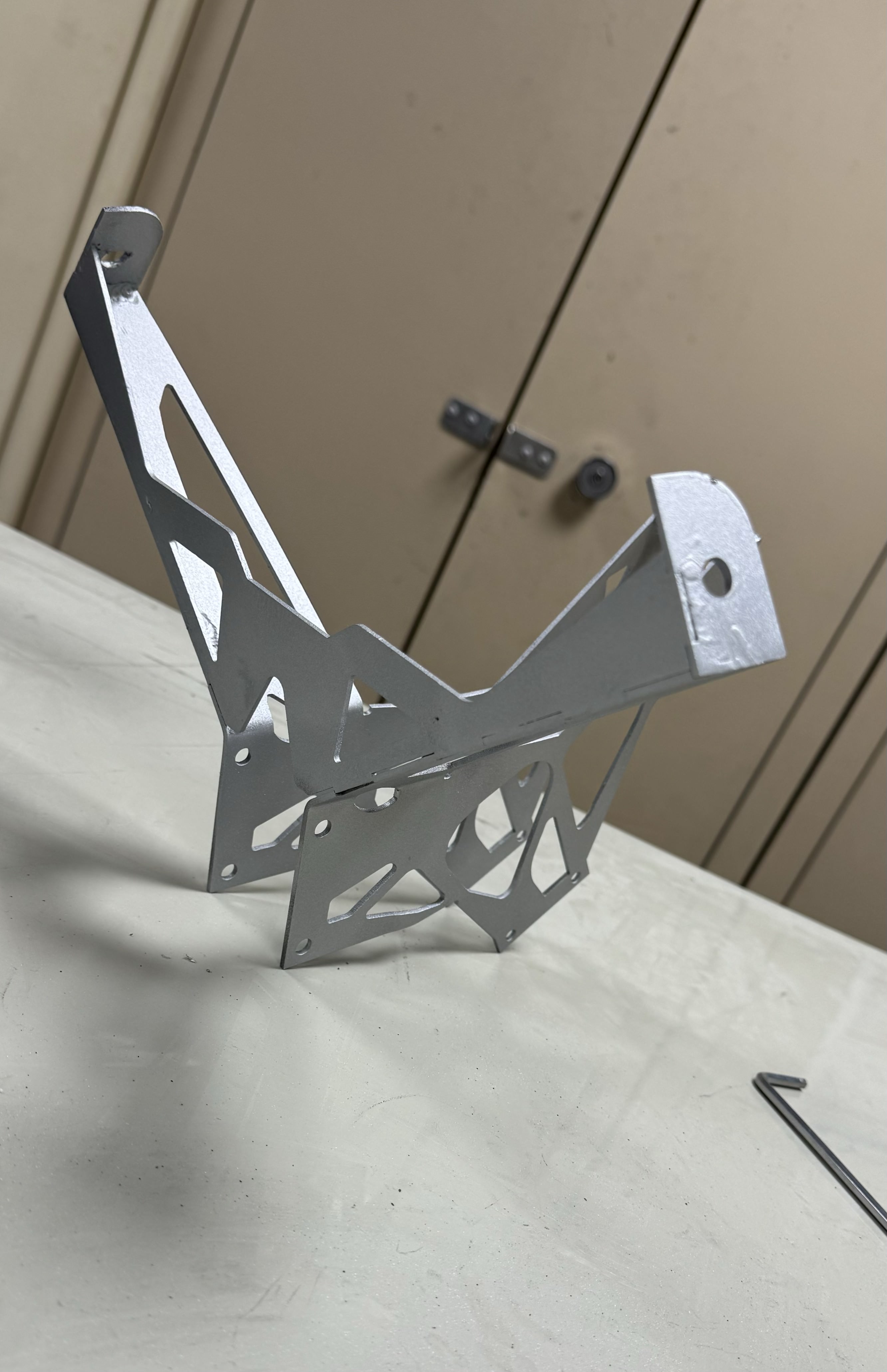
My expertise in CAM allowed me to bring complex designs to life, ensuring precise manufacturing and functionality.
- Programmed and executed milling operations on 3- and 5-axis machines using Top Solid, producing essential parts such as suspension clevises and steering components.
- Tested machining strategies to maximize precision and efficiency during production.
4. Assembly & Testing


I actively contributed to assembling the race car, from chassis integration to dynamic tuning, ensuring the vehicle was competition-ready.
- Assembled key systems, including the monocoque chassis, suspension, steering rack, and electrical harness.
- Conducted electrical setup, enabling quick installation and removal of harnesses within 15 minutes.
- Fine-tuned vehicle parameters (toe, camber, roll bar stiffness) with driver feedback for maximum performance during testing.
5. Project Management & Team Collaboration

Narrative: Working in a multidisciplinary team, I demonstrated strong coordination and problem-solving abilities to deliver results under time constraints.
- Collaborated with frame, aerodynamics, and electrical departments to integrate systems effectively.
- Met tight deadlines, completing the full vehicle design within 3 months.
- Ensured full compliance with FSG 2024 rules, facilitating vehicle approval for dynamic events.
6. Competition Performance

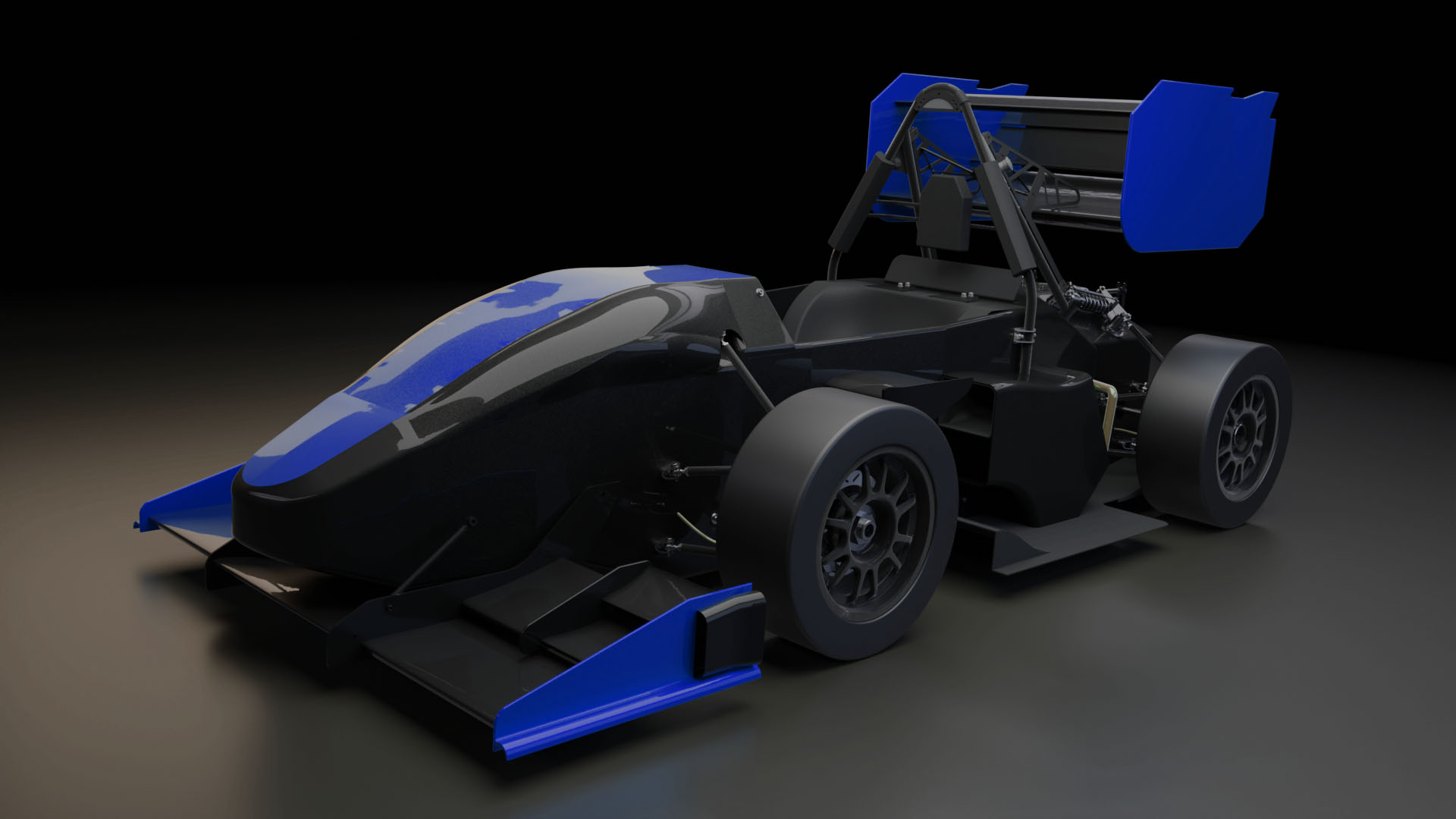
My contributions helped the team achieve success across four international competitions, showcasing innovation and performance.
- Netherlands: Overcame initial compliance challenges during the team’s first competition.
- Spain: Secured 3rd place in the Electric Vehicle category.
- France: Achieved 2nd place in Endurance and 3rd in Autocross events, showcased the vehicle at the Bugatti factory.
- Italy: Completed the competition cycle.